Ready to get more customers calling?
Take FREE Local SEO Course
Available now in English
Kanban - is a project and task management method that originated from lean manufacturing and has been adapted for use in marketing and software development. It is characterised by the visualisation of work, which helps teams to understand the flow of tasks better and manage them effectively.
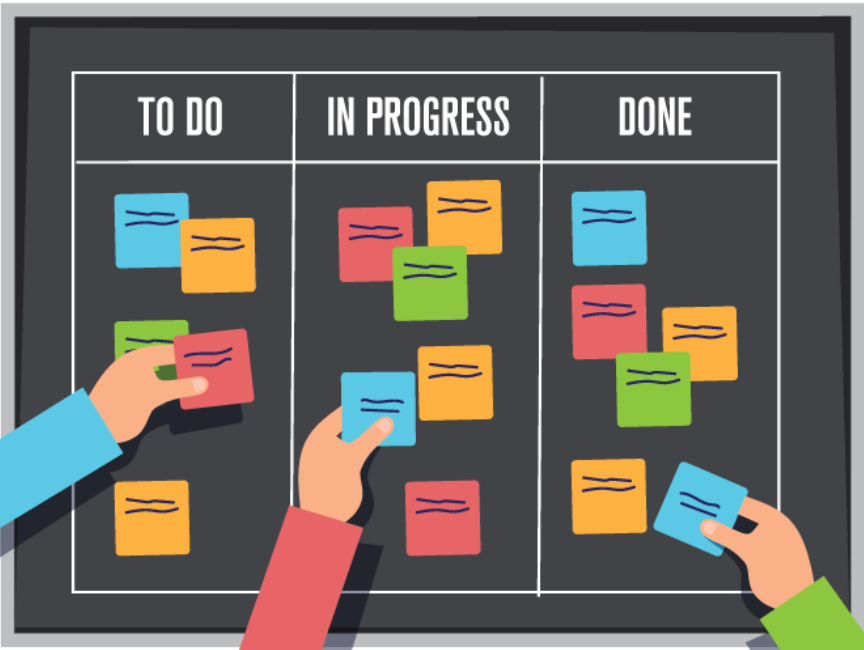
How does the Kanban method work ?
Here are the basic elements of how the Kanban process works:
- Kanban board - the central element is the Kanban board, which can be physical (e.g. a cork board) or digital (e.g. Kanban software). The basic Kanban board is divided into columns corresponding to stages in the work process, such as ‘To Do’, ‘In Progress’ and ‘Completed’.
- Task cards - all tasks are represented by a card containing information such as a description of the task, the responsible person, and deadlines. Cards are placed in the appropriate column on the board depending on the task’s status.
- Workflow - tasks are moved from one column to another, from left to right, according to the progress of the work. This gives the team a clear picture of the project management.
- Work in Progress (WIP) Limitation - Kanban limits the number of tasks in progress simultaneously. This helps prevent the team from being overloaded and ensures a smooth workflow.
- Continuous Adjustment - the Kanban methodology encourages continuous adjustment and optimisation of processes in response to observed problems and bottlenecks.
- Meetings and Communication - regular team meetings (e.g. stand-up meetings) allow the team to update the status of tasks and discuss any problems.
The Kanban method is flexible and can be adapted to different working environments, making it an effective tool in manufacturing as well as in marketing, IT or other service sectors.
Advantages of Kanban practices
There are many advantages to using Kanban, including:
- Improving Workflow - Kanban makes identifying and eliminating downtime and bottlenecks easier, leading to a smoother workflow.
- Increased Efficiency - by reducing the amount of work in progress (WIP), Kanban helps teams focus on completing current tasks instead of starting new ones, which increases efficiency.
- Visualise Progress - the Kanban board provides the team with a clear picture of the current status of projects, making it easier to monitor and manage progress.
- Flexibility - the Kanban method can be adapted to different environments and team needs.
- Encouraging Collaboration - Kanban promotes collaboration and communication within the team, leading to better manufacturing process, work organisation and problem-solving.
- Reducing Waste - Kanban helps identify and eliminate inefficient practices, which reduces wasted time and resources.
- Continuous Improvement - the Kaizen principles in Kanban encourage continuous process improvement, leading to continuous improvement in the quality of work.
- Better Control over Tasks and Projects - Kanban provides better control over tasks and projects, which helps to complete them on time.
- Increased Customer Satisfaction - focusing on continuous improvement and responding quickly to customer needs results in higher quality services and products.
- Increased Transparency - by visualising work, all team members are clear on priorities and responsibilities, increasing process transparency.
Kanban is particularly beneficial in environments that require a high degree of adaptation and rapid response to changing customer requirements.
Lean manufacturing Kanban - Summary
In lean manufacturing, Kanban is a signalling system that alerts you when you need to replenish inventory or start working on new items. Kanban cards, physical or digital, are assigned to individual parts or products and moved along the production chain. When a stage is ready to receive more work, a Kanban card is sent to the previous stage as a signal to start production. The Kanban system helps to keep production flowing, reduces excess inventory and enables rapid response to changing conditions and demand. It is an approach focused on continuous improvement and eliminating waste in every aspect of the production process.